The Bat Man
Colin Henderson learnt to shape cricket bats 40 years ago, and over the years has kept returning to the craft. Now, aged 71, he’s still hands-on creating quality bats.
Colin Henderson learnt to shape cricket bats 40 years ago, and over the years has kept returning to the craft he loves so much. Now, aged 71, he’s still hands-on creating his quality Centurion bats in Tauranga.
Cricket bat craftsman Colin Henderson can’t seem to stay away from willow.
The Tauranga builder already had two runs on the board when son Kayne nudged him back into the workshop, to relaunch a long-held passion project. Now, Colin is doing what he loves for a third time and all three of his children are involved in the family’s Centurion Cricket Co business.
The 71-year-old learned to shape bats almost 40 years ago, while working for the Mount Maunganui franchisee of renowned cricket manufacturer Newbery. Hands-on practical skills came naturally to the former farm boy who already had a carpentry background when he began gauging the shape and weight of a new bat, fashioning and splicing handles then binding them with string, or transforming rubber latex into grips.
“It’s very labour-intensive but it’s satisfying,” he says of his chosen craft. “It’s a lot of fun. And I like working with wood, I suppose.”
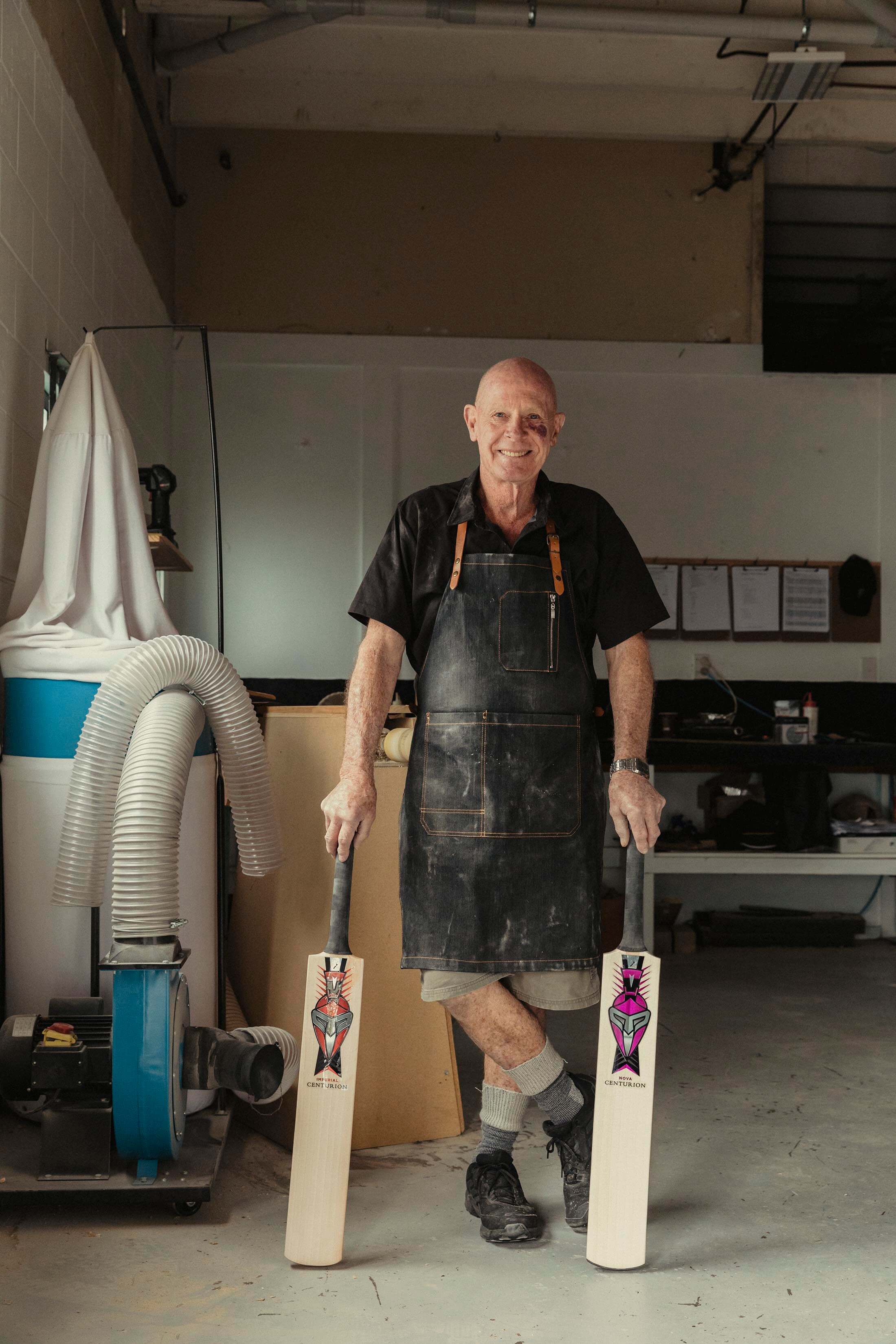
So, when the franchise folded, Colin decided to launch his own brand. He headed to the United Kingdom to visit manufacturers and began importing his own wedges of English willow alongside
the Indonesian cane destined to become handles. The lower level of his Pillans Point house was converted to a workshop and he set to work, sawing and sanding into the night with wife Allison
and three young children — Kayne, Mat and baby Erika — upstairs. Cricket players would also
visit for repairs of old favourites, as well as customised bats that may be heavier or lighter or
longer to suit an individual player’s needs. Colin outgrew the home based premises and two subsequent locations before settling into a commercial building in Greerton, where he made
up to 400 bats a year.
In mid 1980s New Zealand, the national cricket team was enjoying a golden era and Centurion Cricket Co’s fortunes were rising alongside. “Once the national teams starts to go well, everyone wants to play.”
Unfortunately, the reverse is true, too. By 1990, interest in cricket had waned and demand for handmade bats had dropped away. This was despite 19-year-old Jeff Wilson taking the New
Zealand team to a One Day International win against Australia in 1992, wielding a Centurion bat.
So Colin returned to building, took a bread run for six years, did odd jobs and largely shelved
his business until 2015, when son Kayne returned from Europe where he had worked for sporting giant Adidas.
“The boys weren’t really involved in my business before but they both played First XI cricket at Tauranga Boys’ College and loved it. And while he was in Germany, Kayne was heavily involved
with cricket around the world, spending a lot of time with cricketers. When he came home, he
said ‘we’re going to revive Centurion’.
“I was thrilled,” the lifelong cricket fan says. “I said, let’s get back into it.”
Colin is content to remain in his Judea workshop. “As long as my hands stay in shape and I can still work, I’ll stay here and be part of it.”
This time around, the father and son have opted for a business model that has slashed prices while offering the same high quality workmanship and the same personalised service. So, rather than importing blocks of wood and painstakingly shaping each bat from scratch, Centurion buys English willow from India as pre-shaped blanks. Colin then customises and finishes the blanks in his Judea workshop, rasping the handle to perfectly fit a hand or shaving weight from the lower back of a bat so it “picks up” well. Every bat is run through a knocking in machine that delivers 10,000 thumps in half an hour, to break down wood fibres, then oiled and finished to ensure it is game-ready. And the master craftsman continues to repair, rejuvenate and reshape old or damaged bats, while making just a few bespoke specialty bats on the side.
The pair have visited their Indian suppliers east of New Delhi and watched workers shaping the blanks using planes and other hand tools. Centurion also imports Indian-made cricket pads and gloves.
Kanye juggles a day job selling insurance and will sometimes help Colin in the workshop while managing the company website and social media, customer service, finances, stock levels and quality control. Colin laughingly admits to the occasional curt exchange with his exacting oldest
son. “Kayne is a very particular guy, everything’s got to be dead right. I get told off if the labels
aren’t perfectly centred.”
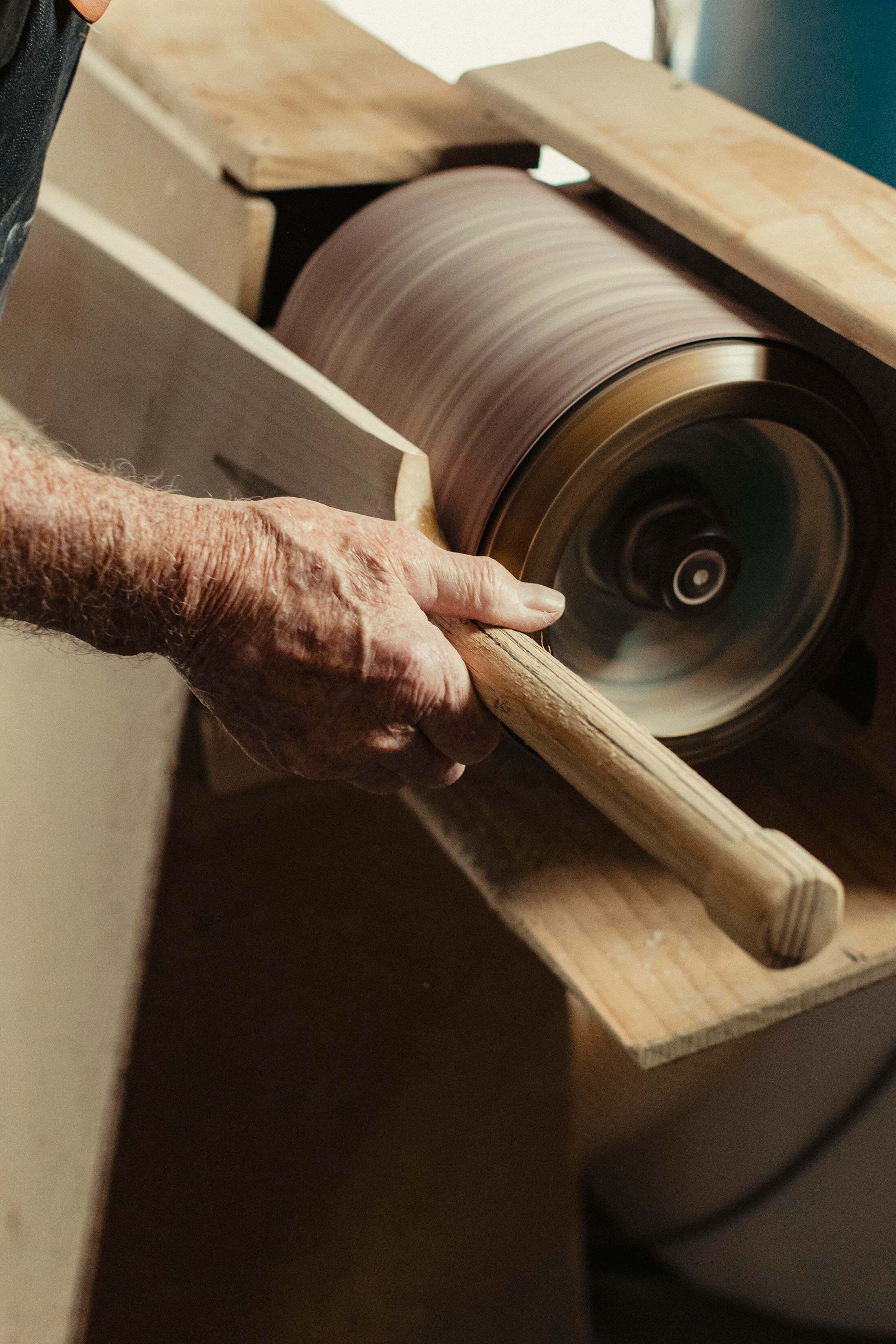
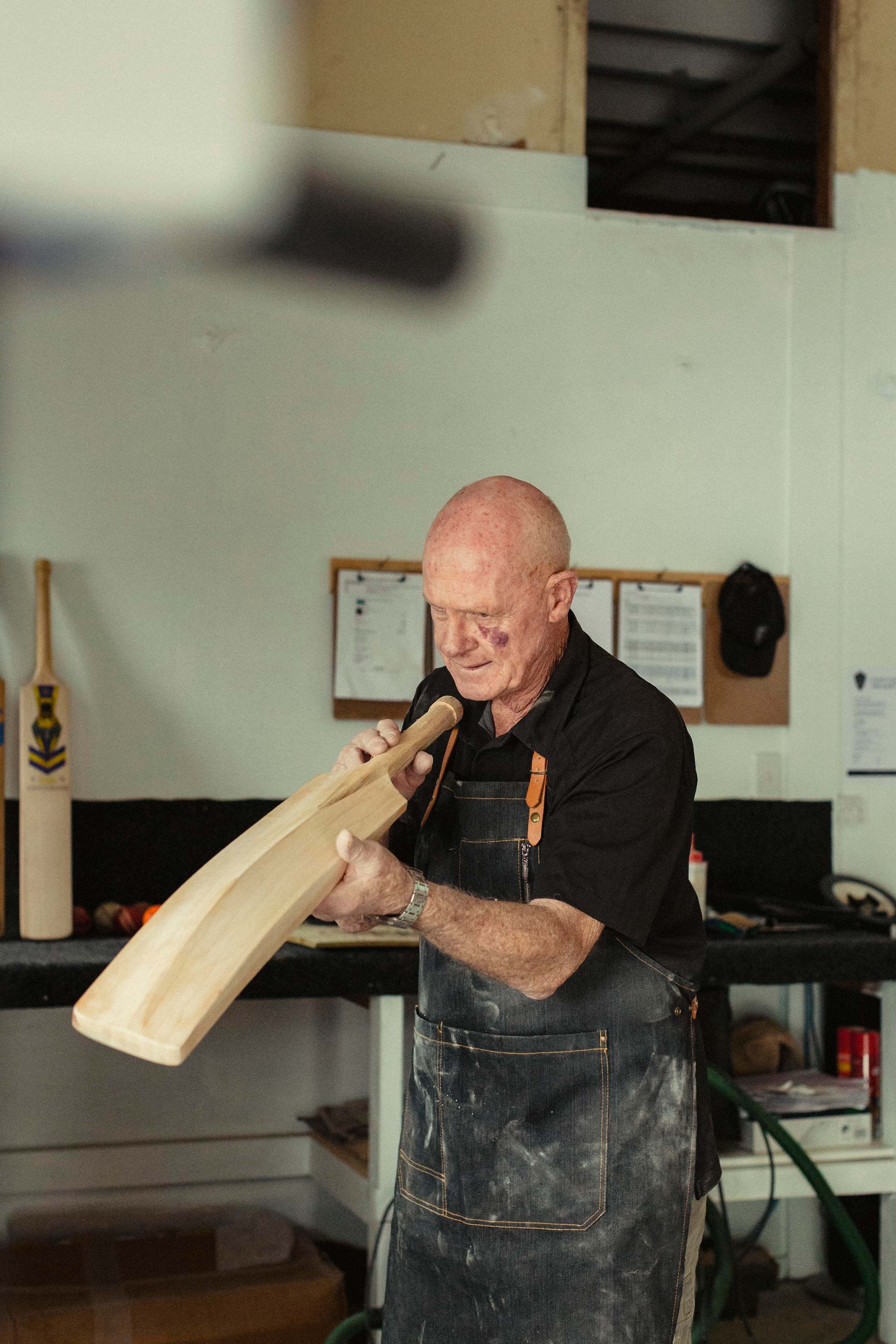
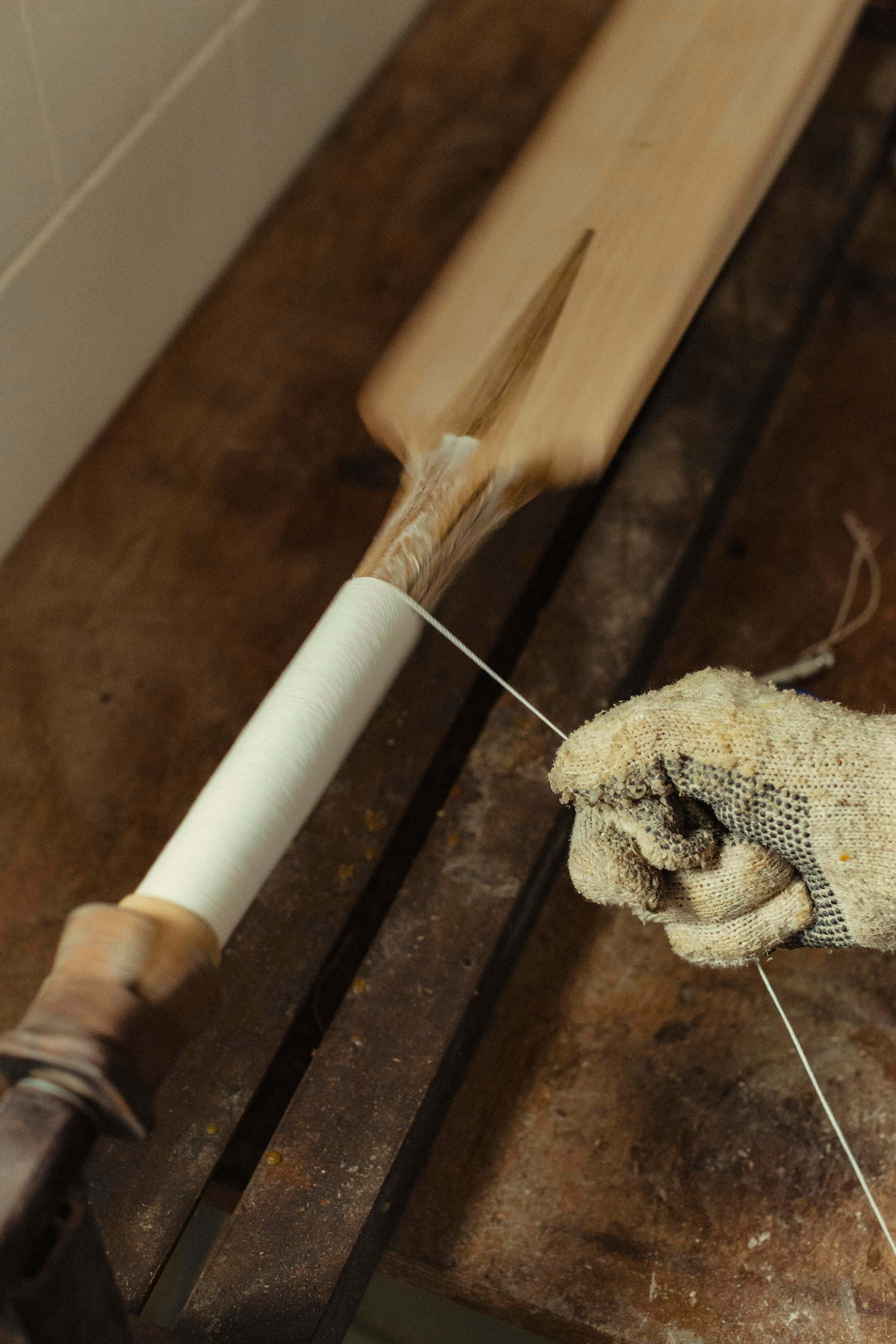
Meanwhile, daughter Erika has taken on the marketing and administration roles while photographer son Mat is in charge of imagery and carries out hands-on repairs in his own New Plymouth workshop.
It’s an effective formula.
“In business, you’ve got to look ahead and see what more you can do or how you can do it differently. That’s where the kids come in. They’re changing things, working on new things, keeping the website up to date. We’ve all got our different parts to play. It’s just satisfying to have all your family involved with you in something they enjoy, too.”
Colin is quick to point out his wife and his children’s partners all chip in and support, too. He is content to remain among the glue and timber and tools in his Judea workshop, or talk with customers in the adjacent showroom.
“As long as my hands stay in shape and I can still work, I’ll stay here and be part of it.”
How to choose a bat
Every would-be Centurion Cricket Co purchaser is encouraged to whack a ball into a net in the converted workshop next door. “Too many people look at a bat and say, ‘oh I like the look of that’,” Colin says. “I say it’s not what it looks like, it’s the way it sounds and the way it feels. Every bat sounds different when you put a ball on it. Some will go clunk. Other bats will ping and the ball will jump off it. “People have to pick out three or four bats that they like, then take some old balls next door and we let them hit the ball until they find the one they like. Suddenly they’ll twig and you can see a smile on their face and you know that’s the one they’re going to take.”
centurioncricket.co.nz
@centurion_cricket_nz
Story by Sue Hoffart
Photography by Adrienne Pitts